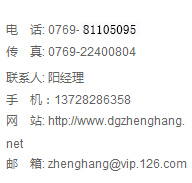
通過以上一系列的研究工作,正航儀器收集整理,從中,本文得到以下結(jié)論:
1、在曲軸轉(zhuǎn)速分別為2600r/min、2400r/min、2000r/min、1600r/min,1400r/min時,穩(wěn)態(tài)仿真兩個工作循環(huán),曲軸旋轉(zhuǎn)四周,分別得連桿頸負(fù)荷、主軸頸負(fù)荷、飛輪前、后端扭矩等仿真結(jié)果,并同主軸頸與軸承座之間是剛性支承和彈性支撐時的仿真結(jié)果進(jìn)行了對比分析,表明支承條件不同,計算結(jié)果會有較大差異,彈性支撐更符合實(shí)際。
2、有限元計算結(jié)果表明發(fā)動機(jī)工作過程中曲軸第3拐連桿頸上油孔附近應(yīng)力集中最大,其維氏應(yīng)力最大值為208MPa。只有單拐模型計算值的1/2。這是由于曲軸約束載荷計算比較準(zhǔn)確,且考慮相鄰缸點(diǎn)火的影響導(dǎo)致應(yīng)力計算值降低。
3、基體材料為48MnV具有3Cr13電弧噴涂層的在軸向載荷下的疲勞性能有相當(dāng)程度的降低。涂層越厚,疲勞性能越差,疲勞極限越低。涂層厚度為0.1mm,0.2mm和0.3mm的試樣,疲勞極限分別降低了9%,11,8%和14%。疲勞性能降低的主要原因是涂層的結(jié)合強(qiáng)度較低,以及噴砂時殘留的鋁氧化物引起疲勞裂紋萌生。
4、曲軸再制造前后疲勞壽命計算以及曲軸疲勞試驗結(jié)果說明傳統(tǒng)的計算過于保守,這不但對曲軸的設(shè)計和優(yōu)化有一定的意義,也說明再制造發(fā)動機(jī)時直接利用曲軸、采用“減材料”或“加材料”即電弧噴涂3Cr13的方式,其壽命是可靠的,足以維持下一個生命周期。
5、經(jīng)500小時冷熱沖擊可靠性試驗后和1000小時和3000小時可靠性循環(huán)試驗后的試樣較少,試驗結(jié)果可能會有偏差,但是其變化趨勢很清楚。極限彎矩和安全系數(shù)隨曲軸臺架強(qiáng)化試驗的時間有所減小,即臺架試驗時間越長,單拐試驗得到的極限彎矩和安全系數(shù)越小,但變化量很小。因為1000小時曲軸臺架強(qiáng)化試驗相當(dāng)于曲軸的一個生命周期,所以本文試驗的結(jié)果表明,曲軸疲勞壽命最少可以維持三個生命周期,即理論上可以再制造三次以上。這和理論計算的結(jié)果相吻合,表明再制造疲勞壽命模型和壽命預(yù)測的正確性。
6、本文提出了一種產(chǎn)品可再制造性模型和評價方法,并通過對發(fā)動機(jī)可再制造性的評價驗證了該模型的有效性和實(shí)用性。但是該評價模型具有一定的局限性。
(1)它只適合于產(chǎn)品設(shè)計具體化以后,即產(chǎn)品的零件數(shù)要已知;
(2)模型是在目前常用的生產(chǎn)條件下發(fā)展的,不適合相差比較大的生產(chǎn)條件。
說了這么多,關(guān)于再制造汽車發(fā)動機(jī)曲軸實(shí)驗相關(guān)總結(jié),以下正航儀器再為您介紹其中主要創(chuàng)新點(diǎn):
1、提出了基于有限元的再制造產(chǎn)品疲勞壽命評估方法和模型。首次利用動態(tài)仿真結(jié)果作為力邊界條件,考慮彈性支撐和相鄰曲拐的相互影響,建立了一個精確的曲軸有限元模型,并通過再制造曲軸剩余壽命計算和試驗驗證,從理論和試驗上驗證汽車發(fā)動機(jī)曲軸大量用來再制造其疲勞壽命是足夠維持下一個生命周期的事實(shí)。這種再制造零件剩余疲勞壽命預(yù)測方法和模型具有典型的示范意義。
2、通過試驗首次對帶有3Cr13電弧噴涂涂層曲軸材料48MnV的疲勞行為進(jìn)行了研究,揭示了該工藝修復(fù)曲軸疲勞壽命有所下降的現(xiàn)象。
3、初步建立了可再制造性的評價方法和模型,并通過對桑塔納2000發(fā)動機(jī)的可再制造性分析,驗證了模型的正確性和實(shí)效性。
總之,為了使評估產(chǎn)品可再制造性達(dá)到工程實(shí)用要求,除了在理論上,即利用本文提出的可再制造性評估模型評估可再制造在技術(shù)上、經(jīng)濟(jì)上和環(huán)境性的可行性,還要通過安全可靠性評估以及可靠性試驗評估產(chǎn)品是否適合可再制造,最后得到適合再制造的產(chǎn)品及零件數(shù)據(jù)庫,數(shù)據(jù)庫反過來又可以輔助評估相似產(chǎn)品或零件是否適合再制造。(本文來源:正航儀器)http://qftd.net